New system addresses 200mm applications with high productivity and low cost of ownership
Munich - ASM International N.V. (Euronext Amsterdam: ASM LINK) today introduced the A400™ DUO vertical furnace system with dual reactor chambers for wafer sizes of 200mm and smaller. The system’s DUAL Boat reactors produce high throughput, increasing reactor utilization to a very high percentage, while ensuring low capex.
“The new A400™ DUO reactor ensures that ASM will extend its position as a leader in the market for Power, Analog, RF, and MEMS applications,” said Hichem M’Saad, ASM Executive Vice President, Global Products. “As 200mm manufacturing began its renaissance, driven by growth in for instance IoT devices, it became clear that our existing furnace technology could still achieve industry-leading results. Combining our technology with the latest innovations in robotics and controls has significantly enhanced the system’s manufacturing capabilities to meet today’s production targets.”
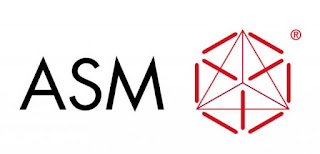
The new DUO is compatible with the original A400™, so existing process recipes can be easily transferred, accelerating system ramp. The system has secured production qualification from multiple customers in Europe, the United States and Asia, including several leaders in power, RF, and MEMS device manufacturing. To date over 20 reactors have been shipped, with a healthy outlook for further shipments.
ASM’s original A400™ vertical furnace system has a proven track record of more than 1000 reactors shipped to customers worldwide and over 25 years of maturity in semiconductor manufacturing. The new system has been modernized to support a variety of growing markets including silicon power, wide band gap semiconductor power, analog, RF and MEMS devices. With its updated control system, software with an intuitive graphical user interface, predictive maintenance by advanced control diagnostics, new robot, and plug-and-play installation, customers can count on the A400™ DUO delivering increased reliability with production output that achieves better repeatability, productivity, and time utilization.
Like its predecessor, the A400™ DUO offers a comprehensive portfolio of process applications including low pressure chemical vapor deposition (LPCVD) processes like doped silicon and silicon nitride films, diffusion processes such as wet oxidation and anneal processes.